Additive Fertigung von multifunktionalen, monolithischen Wandelementen durch Extrusion von Leichtbeton
Bearbeiter: Carla Matthäus, M.Sc.
Förderer: Bundesinstitut für Bau-, Stadt- und Raumforschung (BBSR) in der Forschungsinitiative Zukunft Bau
Zu dem Forschungsprojekt wurde ein Video erstellt, das sie hier ansehen können.
Gegenstand des Vorhabens, das vom Centrum Baustoffe und Materialprüfung gemeinsam mit dem Lehrstuhl für Holzbau und Baukonstruktion der TUM und den Forschungspartnern HeidelbergCement AG, Ed. Züblin AG, Knauf PFT GmbH & Co. KG und Dennert Poraver GmbH bearbeitet wurde, war die Entwicklung eines neuartigen industriellen Bauverfahrens für die automatische und schalungsfreie Herstellung von individuell geformten Bauelementen aus unbewehrtem Leichtbeton.
Mit der additiven Fertigung durch Extrusion von Leichtbeton ist es möglich, schalungsfrei errichtete, thermisch und strukturell optimierte Bauelemente zu fertigen, die ohne zusätzliche Wärmedämmung in der Gebäudehülle eingesetzt werden können. Die für das Projekt gewählten feinen Raupen gewähren dabei eine hohe Auflösung und ermöglichen so die Herstellung von filigranen Hohlraumstrukturen, die die Grundlage für die Funktionalisierung der Bauteile darstellen. Diverse Testobjekte und Demonstratoren wurden hergestellt und damit die Machbarkeit des Verfahrens nachgewiesen.
Die additive Fertigung von Leichtbetonbauteilen kann mittels verschiedener Verfahren realisiert werden. Bei den ablegenden Verfahren (Extrusion) werden die Bauteile durch das Ablegen von Frischbeton frei aufgebaut. Die Extrusion von Beton ist, aufgrund der erreichbaren Festigkeiten und Baugeschwindigkeiten, ein sehr vielversprechender Ansatz zur additiven Herstellung von großformatigen Bauelementen. Die Extrusion erlaubt die Schaffung von geschlossenen, luftgefüllten Hohlräumen, was in Hinblick auf die Optimierung der Wärmedämmfunktion eine wichtige Eigenschaft ist. Gleichzeitig können, verglichen mit anderen ablegenden sowie herkömmlichen Fertigungsverfahren, relativ filigrane Strukturen erzeugt werden. Letzteres ist erforderlich, um die angestrebte Funktionalisierung der Bauteile über eine geometrische Differenzierung zu ermöglichen. Umgekehrt ist die vergleichsweise geringe Rohdichte des Leichtbetons von Vorteil für den Prozess.
Gegenstand des Forschungsvorhabens war somit die Entwicklung eines Verfahrens zur additiven Fertigung von funktionalisierten Wandbauteilen durch Extrusion von Leichtbeton. Frei geformte Bauteiloberflächen von hoher geometrische Auflösung und filigrane Hohlraumstrukturen sollten durch den Einsatz von feinen Düsen möglich gemacht werden. Für alle Komponenten dieses neuartigen Fertigungssystems mussten maßgeschneiderte Lösungen erarbeitet und präzise aufeinander abgestimmt werden.
Einen wesentlichen Teil der Arbeiten stellte die Materialentwicklung dar. Dabei kam ein gefügedichter Leichtbeton, bestehend aus Blähglasgranulat als Leichtzuschlag und Zement als Bindemittel zum Einsatz. Unterschiedliche Faktoren wie Zementart, Zusatzstoffe, w/z-Wert, Korngrößenverteilung des Zuschlags und Zusatzmittel wurden hinsichtlich ihres Einflusses auf die Materialeigenschaften untersucht. Während die Frischbetoneigenschaften insbesondere in Hinblick auf Pumpbarkeit, Baubarkeit, Formtreue und Schichtenverbund optimiert wurden, waren dies bei den Festbetoneigenschaften vor allem Festigkeiten und Wärmeleitfähigkeit.
Parallel zur Materialentwicklung wurde eine an den Werkstoff angepasste, kontinuierlich arbeitende Misch- und Fördertechnik zusammengestellt. Untersuchungen zur Raupengeometrie (Raupenbreite, Schichthöhe und Raupenprofil) mündeten in das Design und die Fertigung von prozessgerecht gestalteten Düsen. Des Weiteren musste eine durchgängige digitale Prozesskette aus Modellier- und Steuerungstools für die Steuerung des Roboters aufgesetzt werden. Der angestrebten Bauteilfunktionalisierung sowie der engen Abhängigkeit zwischen Material, Prozess und Geometrie wird durch speziell gestaltete Schichtenlayouts Rechnung getragen.
Im Laufe des Projektes wurden entsprechend den unterschiedlichen untersuchten Fragestellungen (z.B. Baubarkeit, Formtreue, Oberflächenqualität, Festigkeit, Möglichkeit von Überhängen) eine Vielzahl von Testobjekten gefertigt. Daneben entstanden am Ende der Projektlaufzeit einige großformatige Demonstratoren. Beispielsweise wurde ein Außenwand-Demonstrator mit geschlossenen Zellen erzeugt, bei dem der Wärmedurchgang im Vergleich zu einem herkömmlich hergestellten Bauteil reduziert ist. Wandelemente von 150 cm Höhe (167 Schichten) und einer Grundmaßen von 115 cm x 57 cm wurden in einem Zug innerhalb von 3,5 Stunden gefertigt wurde. Anhand eines 2 m hohen gedrehten Pfeilers mit einer Basisfläche von 69 cm x 69 cm, der innerhalb von 5 Stunden ohne Unterbrechung hergestellt wurde, konnte gezeigt werden, dass wandhohe Elemente ohne Einsatz von Beschleunigern mit dem Verfahren machbar sind. Bei allen genannten Objekten kamen starr montierte runde Düsen mit einem Öffnungsdurchmesser von 15 mm zur Anwendung. Die Schichten haben eine Höhe von 9 mm. Der Entwurf erfolgte direkt über eine geometrische Beschreibung des Extrusionspfades. Die digitalen Modelle sind parametrisch aufgebaut und können unmittelbar in Steuerbefehle für den Roboter umgesetzt werden. Mit diesem Setup war es möglich, schnell auf geänderte Vorgaben aus der Material- und Prozessentwicklung zu reagieren und Erkenntnisse aus vorangegangenen Versuchen zu berücksichtigen.
Während in vielen Industriezweigen die additiven Fertigungsverfahren (3D-Drucken) bereits zum Stand der Technik gezählt werden können, befindet sich ihre Anwendung im Bauwesen noch in den Anfängen. Jedoch gerade für das Bauen, wo Einzelfertigung und geometrische Komplexität die Regel darstellen, birgt diese Zukunftstechnologie gewaltige Potenziale, insbesondere für eine automatische Fertigung von individualisierten Bauteilen. Es kann daher davon ausgegangen werden, dass additive Fertigungsprozesse langfristig auch in der Bauindustrie zu fundamentalen Veränderungen führen werden.


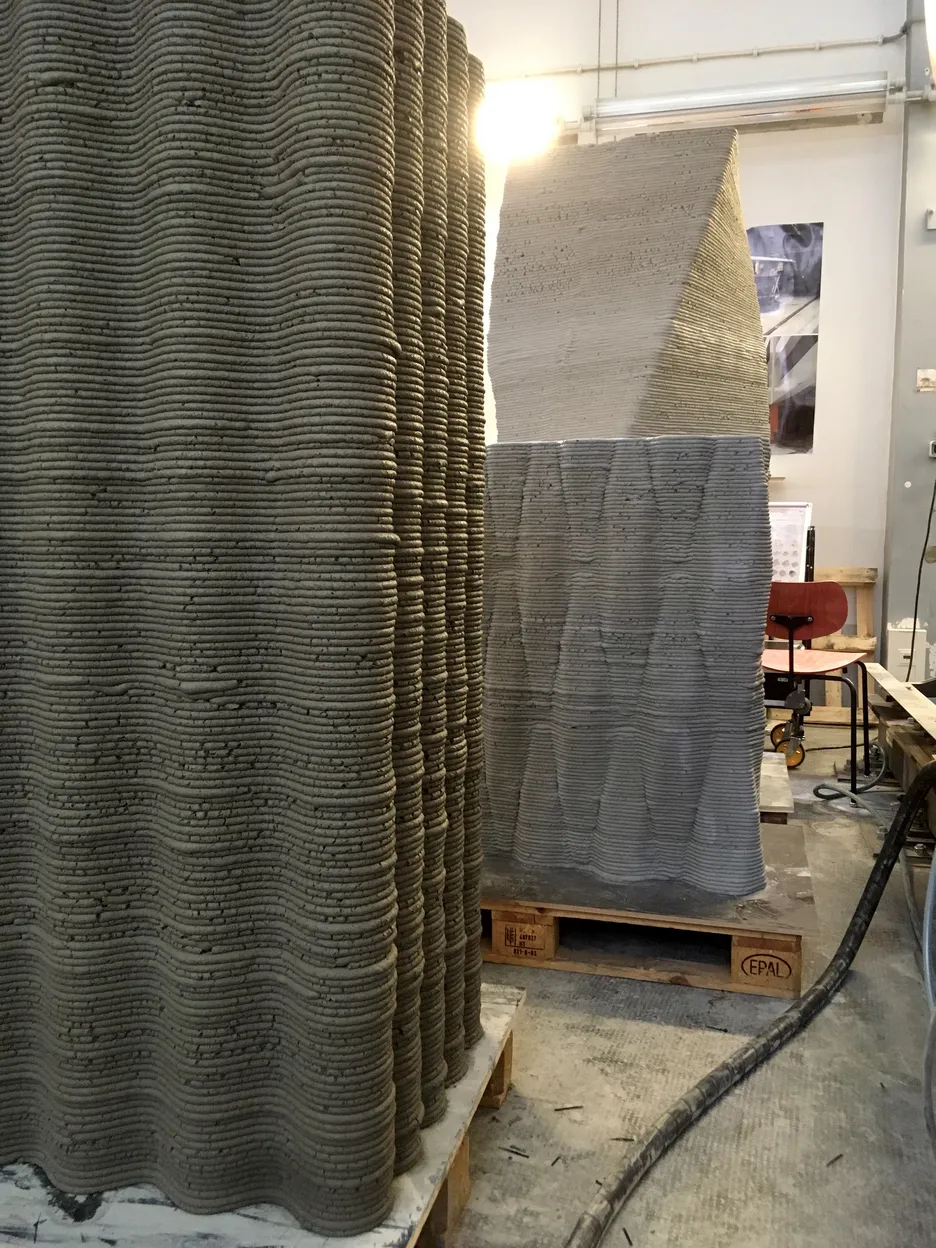